School of Mechanical Engineering (Jun – Jul 2022)
PhD Awards
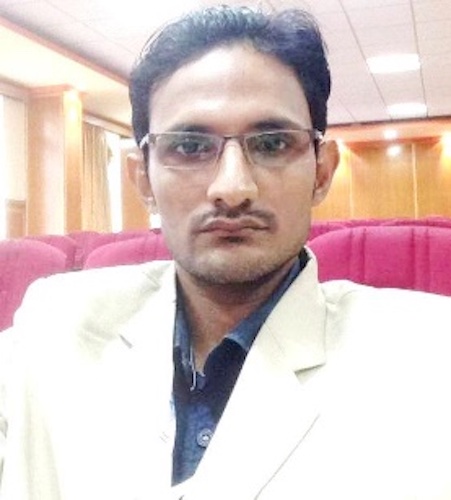
Scholar’s Name: Dr. Samarjit Swain
Supervisor’s Name: Dr. Isham Panigrahi, Assoc. Professor, SME, KIIT Deemed to be University & Dr. Ashok K. Sahoo, Professor & Director R&D (SoT), SME, KIIT Deemed to be University
Thesis Title: Experimental investigation on the machinability of AISI 1040 steel and titanium alloy (Ti-6AI-4V) under dry and MQL environment considering machining parameters and tool vibration
Abstract Current research focused on machinability investigation of AISI 1040 steel and Ti-6Al-4V alloys under dry and MQL environmental condition. Uncoated carbide of ISO geometry CNMG 120408 insert has been implemented for turning of both AISI 1040 steel and Ti-6Al-4V alloys. Three different machining variables namely cutting speed (v), axial feed rate (f), and depth of cut (d) with their three levels are utilized for the experimentation. For dry turning of AISI 1040 steel and MQL turning of Ti-6Al-4V alloys, the input term cutting speed and for dry turning of Ti-6Al-4V alloys depth of cut is found to be the most affecting term for tool flank wear. For dry and MQL machining of Ti-6Al-4V alloy, the input term axial feed rate is the dominant term towards surface roughness, while under dry turning of AISI 1040 steel, cutting speed is the dominant term for surface roughness. For dry turning of AISI 1040 steel and Ti-6Al4V, the input term axial feed rate is the dominant term towards amplitude of vibration signal, while under MQL machining of Ti-6Al-4V alloys, cutting speed is the dominant term for amplitude of vibration signal. Further, the optimal setting for machining of AISI 1040 steel was found as cutting speed = 300 m/min, axial feed rate = 0.06 mm/rev and depth of cut = 0.5 mm. |
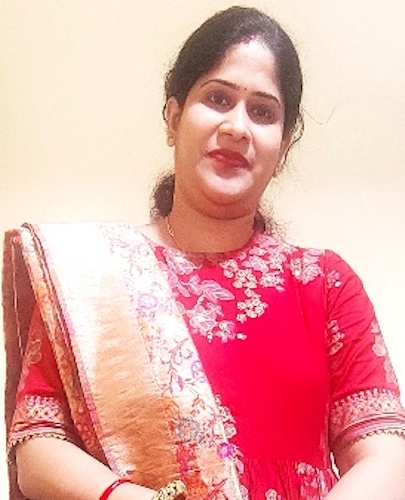
Scholar’s Name: Dr. Smaranika Nayak
Supervisor’s Name: Dr. Isham Panigrahi, Assoc. Professor, SME, KIIT Deemed to be University & Dr. Ramesh Kumar Nayak, Asst. Professor, NIT, Bhopal
Thesis Title: Flexural, Impact, and Tribological Properties of Carbon/Glass Fibre Reinforced Polymer Hybrid Nanocomposite
Abstract The new generation technology is trending towards gradual replacement of conventional metallic materials with fiber reinforced polymer composite materials in various sectors ranging from automotive to aerospace to biomedical applications. The fiber reinforced polymer composite materials are extensively used due to its advantageous properties like high strength, stiffness, high fracture toughness, good corrosion resistance, high impact resistance, limited number of joints, durability, easy manufacturing processes and lighter in weight. Glass fiber reinforced polymer composites (GFRP) possesses lesser strength in comparison to carbon fiber reinforced composites (CFRP) but it is comparatively cheaper in cost. The overall mechanical and tribological properties of the hybrid nanocomposite increased at 5 wt. % of nanoclay. The low velocity impact resistance also reveals optimum energy absorption with reduced damage area for hybrid nanocomposite ([C2G8]) against other composites. The protective side body guards of automobiles were developed using the outcome of the research for future commercialization. Furthermore, fractography analysis was carried out by visual inspection and scanning electron microscope to make possible structure property relationship. The optimum mechanical and tribological properties along with low cost of hybrid composite are found to be suitable for different engineering applications. |
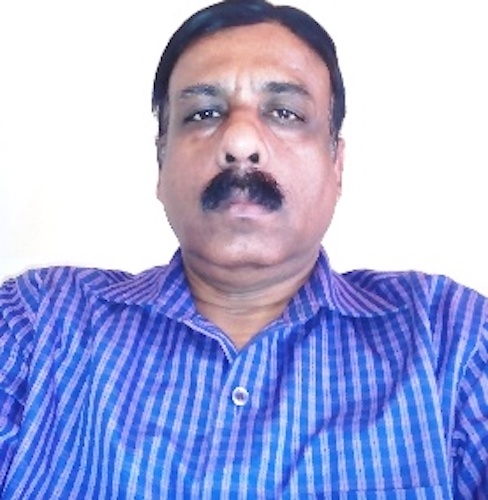
Scholar’s Name: Dr. Ajay Kumar Sahu
Supervisor’s Name: Dr. Prakash Ghose, Asst. Professor, SME, KIIT Deemed to be University
Thesis Title: Computational modeling of pulverized coal combustion to investigate NO reduction using methane as reburn fuel
Abstract The importance of blending of imported and domestic coal is increasing at current scenario in India. Since so many years, the blending has been doing in order to cost cutting by using readily available cheap Indian coal. Today coal blending is becoming apparent because blends provide better heat along with less air and water pollution. The presence of inherent nitrogen and sulphur causes oxides of nitrogen (NOx) and (oxides of sulphur) SOx pollutant during combustion. Blending may also can reduce NOx and SOx. It is even possible to maximize the ash reduction through blending of low ash coal with high ash coal. Dry ash is an air pollutant which pollutes the air inhaled by the local community. Bottom ash that is generally stored in ash pond, sometime damage the crop fields nearby due to overflow or braking of ash pond. In addition to that a fraction of ash melts and sticks on the furnace wall as well as steam pipelines (slagging). Therefore in order to minimize both NOx and ash, in this work it is planned to use methane as a co- fuel by eliminating the Fuel NO particularly. However there are other sources of NO such as; Thermal NO and prompt NO, which are independent of nitrogen present in fuel. Even if Fuel NO contributes a major fraction of total NO, but flame temperature and equivalence ratio also plays an important role to form Thermal NO and Prompt NO. Therefore blending cannot confirm that by increasing of nitrogen free fuel in a pulverized coal combustor, NOx formation will deteriorate. That is the reason, in this work, the effect of blending of methane with coal in various way will be studied computationally to predict the total NO formation. Moreover NO re-burn is also reduces the NO, which again depends on hydrocarbon radicals. Therefore equivalence ratio is also play a major role for NO depletion. |
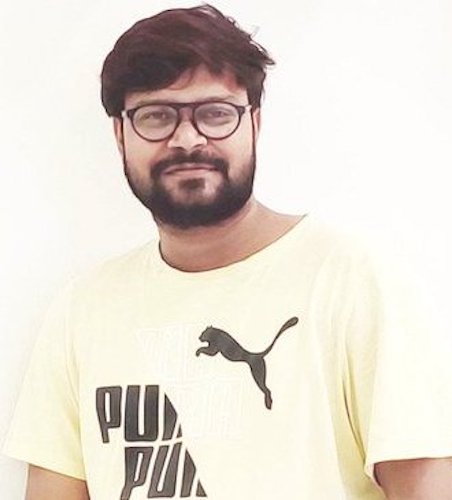
Student’s Name: Dr. Pramod Mandal
Supervisor’s Name: Dr. Sudesna Roy, Assoc. Professor, SME, KIIT (Deemed to be University) & Dr. Udai P. Singh, Sr. Professor, SEE, KIIT (Deemed to be University)
Thesis Title: Investigate the structural, optical and electrical properties of β-gallium oxide thin films deposited by physical vapour deposition (PVD)
Abstract PVD powered by RF sputtering is most widely used technique for depositing thin films from nanometer to micrometers range with smooth and uniform surface finish. This method has been very popular among scientist, researcher, and engineer for fabrication oxide, ceramic, composite, and rare earth oxide with lots of advantages and few demerits. Advantages are easy operation, thickness control with varying its parameters, complicated shape fabrication etc. However it includes demerits such as target materials may get damage over frequent usage. In this report β-gallium oxide was grown on different types substrates such as soda lime glass, quartz for investigation surface morphology, phase analysis, electrical properties, and optical properties for opto-electronics devices. β-gallium oxide(Ga2O3) is very popular semiconductor materials known for their wide band gap of -4.9-5.3 eV in field of optoelectronics, optical, magneto-electronics, photonics and electronics for manufacturing various opto-electronics device such as ultraviolet photo detectors, gas and chemical sensors, solar blind deep ultraviolet detector, piezo-electric device and luminescent devices. |
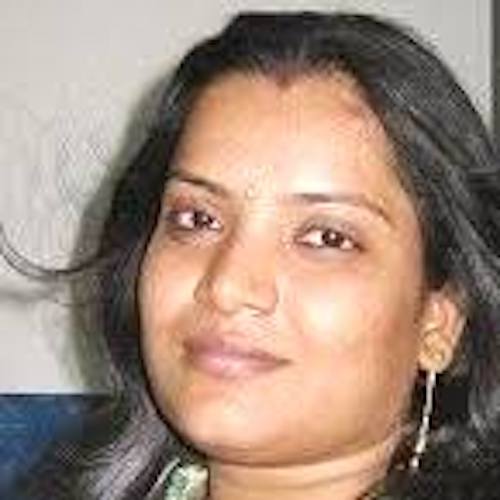
Student’s Name: Dr. Sushmita Dash
Supervisor’s Name: Dr. Trupti Ranjan Mahapatra, Associate Professor, VSSUT Burla & Dr. Isham Panigrahi, Associate Professor, KIIT (Deemed to be University)
Thesis Title: Numerical Analysis of static and free vibration behaviour of functionally graded material sandwich shell panel
Abstract In this work, a higher-order finite element formulation is proposed and developed to compute the static and free vibration responses of functionally graded (FG) material sandwich doubly curved shell panels. The structural model is developed in the framework of a variationally consistent higher-order mid-plane kinematic relation allowing for parabolic variation of transverse shear stress and devoid of the necessity of shear correction factor. Variational principle is employed to derive the system of equations of the panel structure. The present shell panel model is discretized using a quadrilateral Lagrangian isoparametric element with nine nodes and each node associated with nine degrees of freedom. Own MATLAB computer code is written vie with the proposed higher-order finite element scheme to calculate the desired responses. Admirable stability of the present numerical model for computing the central deflection and natural frequency of vibration for single and doubly curved FG sandwich shell panels is established via the convergence test. Further, close conformance of the present results for FG sandwich plates of diverse symmetries is also found when compared with the theoretical predictions based on other theories as well as 3D elasticity solutions. Subsequently, appropriate numerical examples are solved pertaining to various design factors (curvature ratio, core-face thickness ratio, aspect ratio, support conditions, power-law index and sandwich symmetry type) those have significant influence on the flexural and free vibration responses of FG sandwich curved panels and the useful inferences are discussed in detail. |
Journal papers
1. Mukherjee, S., Mishra, P. C., Ali, N., Aljuwayhel, N. F., Ebrahim, S. A., & Chaudhuri, P. (2022). Thermo-physical properties and heat transfer potential of novel silica-ethylene glycol mono nanofluid: Experiments and multi-layer perceptron (MLP) modelling. Colloids and Surfaces A: Physicochemical and Engineering Aspects, 648, 129412. https://doi.org/10.1016/j.colsurfa.2022.129412 (Impact Factor: 5.518)
Abstract
The aim of this research is to estimate the thermophysical properties and heat transfer potential of silica-ethylene glycol (EG) mono nanofluid. Silica nanoparticles were dispersed in pure ethylene glycol in four different concentrations of 0.01, 0.05, 0.10 and 0.50 vol. % via two-step method. The dispersion stability of the nanofluid was enhanced including Gum Arabic (GA) as surfactant. Colorimeter and Zeta potential analyses were employed to determine the stability of the as-prepared samples. Thermal conductivity of nanofluid was determined by innovative sonic velocity measurement technique. Viscosity was measured by capillary viscometer. The highest augmentation in thermal conductivity was found to be 19.19 % at 60 °C and in viscosity was found to be 5.07 % at 40 °C with the 0.50 vol. % SiO2 particle dispersion. A set of new data fitting-based correlations and optimal multi-layer perceptron (MLP) models for thermal conductivity and viscosity of Silica-EG nanofluids with high prediction capacities (R-square > 90 %) were proposed based on the experimental data. The MLP models were more accurate than fitting models. Evaluation criterion was implemented to estimate the potential heat transfer of nanofluid.
2. Mukherjee, S., Mishra, P. C., Chakrabarty, S., & Chaudhuri, P. (2022). Effects of sonication period on colloidal stability and thermal conductivity of SiO2–water nanofluid: An experimental investigation. Journal of Cluster Science, 33(4), 1763-1771. https://doi.org/10.1007/s10876-021-02100-w (Impact Factor: 3.447).
Abstract
The objective of the present work is to analyze the consequences of the sonication period on the colloidal stability and thermal conductivity of SiO2–water nanofluid. Ultrasonication assisted two-step method was applied to prepare SiO2–water nanofluid at two different concentrations of 0.5 and 1 wt% without any surfactant. The sonication period varied from 1 to 3 h. Particle size was analysed by direct light scattering (DLS). Zeta potential analysis and light absorbance test were performed to check the colloidal stability of nanofluids. The thermal conductivity of nanofluid was measured over the temperature range of 25–60 °C. The obtained results indicate that increasing sonication time is crucial for the enhancement in stability and thermal conductivity of nanofluid. With increasing temperature, the thermal conductivity of nanofluids also increased. Moreover, at lower temperature, sonication plays a dominant role on thermal conductivity enhacement in nanofluids. The investigation concludes that a minimum 2.5 h of sonication is required for the better performance of nanofluids.
3. Khadanga, V., Mukherjee, S., Mishra, P. C., & Chakrabarty, S. (2022). Heat Transfer Performance of Novel SiO2 Nanoaerosol: The Numerical Investigation. Microgravity Science and Technology, 34(3), 1-8. https://doi.org/10.1007/s12217-022-09969-w (Impact Factor: 1.642).
Abstract
Presently nanoaerosol technology has widened its application in the heat transfer area and found to be exhibiting remarkable heat transfer characteristics. This paper focuses on a theoretical investigation on the convective heat transfer characteristics of a SiO2-air nanoaerosol flow inside a tube. Based on the properties of nanoparticles and air, the governing equations and numerical models have been formulated and simulations are carried out. The distribution of temperature in terms of time scale within SiO2 nanoparticles, particle to particle interaction through conduction, and nanoparticles to air by radiation is studied. At particle diameters, 30 nm to 120 nm, the timescale of particle, conduction, and radiation are compared, and it was that the temperature distribution in conduction is more rapid than radiation. Aerosol heat transfer coefficient (AHTC) at different Reynolds number (Re) from 8,000 to 20,000, with different particle volume fractions (PVF) from 0.002 to 0.01 has been investigated. Moreover, the effect of the particle migration factor on AHTC has been analysed. However, PVF has very mild effect on AHTC. A maximum of 51.96% enhancement in AHTC was observed by increasing Re from 8,000 to 20,000. Thus, the nanoaerosol has potential in gaseous cooling applications.
4. Mukherjee, S., Aljuwayhel, N. F., Bal, S., Mishra, P. C., & Ali, N. (2022). Modelling, analysis and entropy generation minimization of Al2O3-Ethylene Glycol nanofluid convective flow inside a tube. Energies, 15(9), 3073. https://doi.org/10.3390/en15093073 (Impact Factor: 3.252).
Abstract
Entropy generation is always a matter of concern in a heat transfer system. It denotes the amount of energy lost as a result of irreversibility. As a result, it must be reduced. The present work considers an investigation on the turbulent forced convective heat transfer and entropy generation of Al2O3-Ethylene glycol (EG) nanofluid inside a circular tube subjected to constant wall temperature. The study is focused on the development of an analytical framework by using mathematical models to simulate the characteristics of nanofluids in the as-mentioned thermal system. The simulated result is validated using published data. Further, Genetic algorithm (GA) and DIRECT algorithm are implemented to determine the optimal condition which yields minimum entropy generation. According to the findings, heat transfer increases at a direct proportion to the mass flow, Reynolds number (Re), and volume concentration of nanoparticles. Furthermore, as Re increases, particle concentration should be decreased in order to reduce total entropy generation (TEG) and to improve heat transfer rate of any given particle size. A minimal concentration of nanoparticles is required to reduce TEG when Re is maintained constant. The highest increase in TEG with nanofluids was 2.93 times that of basefluid. The optimum condition for minimum entropy generation is Re = 4000, nanoparticle size = 65 nm, volume concentration = 0.2% and mass flow rate = 0.54 kg/s.
5. Jena, M., Mishra, P. C., & Sahu, S. S. (2022). Comparative performance of jet and spray impingement cooling in steel strip run-out table: experimental results. Australian Journal of Mechanical Engineering, 1-14. https://doi.org/10.1080/14484846.2022.2066854
Abstract
This paper presents a comparative performance study of cooling techniques based on air-assisted water spray and jet impingement for heated moving metallic plates. To achieve the heat transfer characteristics of spray and jet cooling methods, an experimental setup was developed to accommodate the spray (SIC) and jet impingement cooling (JIC). The temperature at different locations of the plate was taken by K-type thermocouples embedded therein and attached to CHINO-make data acquisition system. The cooling curves obtained were utilised for computing the cooling rates. Experiments were conducted by varying the parameters, e.g. pressure of air and water, distance between plate and nozzle tip and speed of plate as per Taguchi design of experiments. The results revealed that SIC has great advantage over the JIC method under the same thermal conditions. There was a fall of cooling rate with increase in plate thickness for both SIC and JIC. The requirement of shorter length of run-out table (ROT) in case of SIC has established the cost effectiveness of using SIC compared to JIC. The cooling process played a critical role in steel manufacturing industry where the determined cooling rates evaluated the setup costs during planning phase of the project.
6. Mukherjee, S., Ebrahim, S., Mishra, P. C., Ali, N., & Chaudhuri, P. (2022). A review on pool and flow boiling enhancement using nanofluids: Nuclear reactor application. Processes, 10(1), 177. https://doi.org/10.3390/pr10010177 (Impact Factor: 3.352).
Abstract
Plasma-facing components (PFCs) are used as the barrier to the beam of high heat flux generated due to nuclear fusion. Therefore, efficient cooling of PFCs is required for safety and smooth operation of a fusion reactor. The Hyper Vapotron (HV) is generally used as the heat exchanger to cool down the PFCs during operation. These heat exchangers use pool and flow boiling mechanisms, and hence, their ability is inherently constrained by critical heat flux (CHF). The boiling of nanofluid is very promising as the working fluid in the HV. The efficiency of the HV increases due to the increase in CHF by applying nanofluids. However, the feasibility of nanofluid cooling in fusion reactors needs proper understanding. This paper reviews the recent developments in the utilization of boiling phenomena in nanofluid as a coolant in the HV. Experiments, theoretical studies, significant achievements, and challenges are analyzed and discussed. Finally, important points are indicated for future research.
7. Rajan, K. M., Kumar Sahoo, A., Chandra Routara, B., & Kumar, R. (2022). Investigation on surface roughness, tool wear and cutting power in MQL turning of bio-medical Ti-6Al-4V ELI alloy with sustainability. Proceedings of the Institution of Mechanical Engineers, Part E: Journal of Process Mechanical Engineering, 236(4), pp. 1452–1466. https://doi.org/10.1177/09544089211063712 (Impact Factor: 1.761).
Abstract
Ti-6Al-4V ELI (Grade 23) is highly recommended for bio-materials and due to its low thermal conductivity and a chemically reactive property, machinability is poor. Thus the current work emphasized on the selection of appropriate cooling technique and optimal cutting parameters for machining of Ti-6Al-4V ELI alloy with sustainability analysis for surface roughness, flank wear and cutting power. Initially, the cutting performances under dry, flood and MQL environments are compared and MQL is observed to better performed. At lower speed (70 m/min), MQL exhibited 26.38% and 19.69% lesser surface roughness relative to dry and flood cooling individually. At the same cutting condition, MQL assisted cutting resulted in lower flank wear relative to dry (157. 33%) and flood cooling (40%). Further, a detailed investigation has been made under MQL through Taguchi L18 design of experiments. The major mechanisms for flank wear are found to be abrasion, chipping and notch wear. Optimal data set through Grey relational analysis is found to be v1 (70 m/min), f1 (0.1 mm/rev) and d1 (0.1 mm) and improved. Quadratic regression model is found to be significant for prediction of responses. Sustainability Pugh matrix assessment revealed that MQL environment enhanced the economical, technological as well as environmental and operator health aspects. Reduction of energy consumption by 53.96% and savings of carbon footprints by 68.46 kg of CO2 observed under MQL at optimal conditions and thus saves manufacturing cost.
8. Swain, S., Kumar, R., Panigrahi, I., Sahoo, A. K., & Panda, A. (2022). Machinability performance investigation in CNC turning of Ti-6Al-4V alloy: Dry versus Iron-aluminum oil coupled MQL machining comparison. International Journal of Lightweight Materials and Manufacture, 5(4), 496–509. https://doi.org/10.1016/j.ijlmm.2022.06.002
Abstract
Ti–6Al–4V is the largest useable titanium grade alloy in various engineering components due to its superior inherent properties like high strength to weight ratio, highly corrosive resistance, ability to withstand high temperature, etc. But machining of this alloy is found to be challenging because of having lesser thermal conductivity, highly chemical sensible, more sensitivity in work hardening and low young’s modulus. However, the current study offers the use of novel and environment pleasant lubricants like iron aluminum oil with minimum quantity lubrication (MQL) concept to machine this alloy using a low budget hard tool (uncoated carbide) and the performance was compared with dry machining. Severe abrasion, adhesion, diffusion, and chipping were the main cause of tool failure in both cooling strategies. The tool life in MQL was traced to be 280% greater than the dry condition at the same turning parameters. Compared to dry turning, lower tool vibration and superior surface quality were obtained in MQL. The MQL assisted turning exhibited 12.38% lower costs than dry. Overall, with the use of an uncoated carbide tool, the turning of Ti–6Al–4V alloy in MQL was found to be more precise and more economical than dry and recommended for mass production works.
9. Kumar, R., Gour, S. S., Pandey, A., Kumar, S., Mohan, A., Shashwat, P., & Sahoo, A. K. (2022). Design and Analysis of a Novel Concept-Based Unmanned Aerial Vehicle with Ground Traversing Capability. Acta Mechanica et Automatica, 16(3), 169-179. https://doi.org/10.2478/ama-2022-0021
Abstract
Unmanned aerial vehicle (UAV) is a typical aircraft that is operated remotely by a human operator or autonomously by an on-board microcontroller. The UAV typically carries offensive ordnance, target designators, sensors or electronic transmitters designed for one or more applications. Such application can be in the field of defense surveillance, border patrol, search, bomb disposals, logistics and so forth. These UAVs are also being used in some other areas, such as medical purposes including for medicine delivery, rescue operations, agricultural applications and so on. However, these UAVs can only fly in the sky, and they cannot travel on the ground for other applications. Therefore, in this paper, we design and present the novel concept-based UAV, which can also travel on the ground and rough terrain as an unmanned ground vehicle (UGV). This means that according to our requirement, we can use this as a quad copter and caterpillar wheel–based UGV using a single remote-control unit. Further, the current study also briefly discusses the two-dimensional (2D) and three-dimensional (3D) SolidWorks models of the novel concept-based combined vehicle (UAV + UGV), together with a physical model of a combined vehicle (UAV + UGV) and its various components. Moreover, the kinematic analysis of a combined vehicle (UAV + UGV) has been studied, and the motion controlling kinematic equations have been derived. Then, the real-time aerial and ground motions and orientations and control-based experimental results of a combined vehicle (UAV + UGV) are presented to demonstrate the robustness and effectiveness of the proposed vehicle.
10. Kumar, R., Pandey, A., Sahoo, A. K., & Rafighi, M. (2022). Investigation of machinability performance in turning of Ti–6Al–4V ELI alloy using firefly algorithm and GRNN approaches. Surface Review and Letters, 29(6), 2250075. https://doi.org/10.1142/S0218625X22500755 (Impact Factor: 1.240).
Abstract
Ti–6Al–4V ELI alloy is one of the most familiar materials for orthopedic implants, aeronautical parts, marine components, oil and gas production equipment, and cryogenic vessel applications. Therefore, it’s appropriate quality of finishing is highly essential for these applications. But the characteristics like lower modulus of elasticity, lesser thermal conductivity, and high chemical sensitivity placed it in the categories of difficult-to-cut metal alloys. Also, tooling cost is one of the prime issues in the machining of this alloy. Therefore, this research is more inclined to use a low-budget uncoated carbide tool in turning the Ti–6Al–4V ELI alloy. Also, the selection of suitable levels of machining parameters is highly indispensable to get the appropriate surface finish with a low tooling cost. So, the L16 experimental design is utilized to check the performances of the uncoated carbide tool in the turning tests. The performance indexes like surface roughness (Ra), flank wear of tool (VBc), and material removal rate (MRR) are measured and studied with the help of surface plots and interaction plots. Further, the Firefly Algorithm optimization is employed to find the optimal cutting parameters and cutting response values. The local optimal values of the input parameters a, f, and Vc are estimated as 0.3241mm, 0.0893mm/rev, and 82.41m/min, respectively. Similarly, the global optimal values for the responses Ra, VBc, and MRR are reported as 0.6321μm, 0.09253mm, and 24.61g/min, individually. Additionally, to predict the responses, Generalized Regression Neural Network (GRNN) modeling is employed and the average absolute error for each response is noticed to be less than 1%. Therefore, the GRNN modeling tool is strongly recommended for various machining applications.
11. Soren, T. R., Kumar, R., Pandey, A., Sahoo, A. K., Panigrahi, I., & Panda, A. (2022). Machinability investigation of high-strength 7068 aluminum alloy: a potential study through experimentation, spotted hyena optimization and advanced modeling approaches. Surface Review and Letters, 29(06), 2250081. https://doi.org/10.1142/S0218625X22500810 (Impact Factor: 1.240).
Abstract
This research emphasizes the machinability investigation on CNC turning of 7068 aluminum alloys. CVD-coated carbide tool was implemented for the L27 full-factorial-based turning experiments in dry conditions. Machinability study includes the assessment of flank wear, cutting tool vibration, surface roughness, cutting temperature, chip reduction coefficient, and chip morphology. The selected tool performed well as very low wear (0.030–0.045mm) and low surface roughness (0.28–1.14μm) were found. All the input variables have significant impact on the flank wear, cutting tool vibration, cutting temperature, and chip reduction coefficient while for surface roughness, the effects of cutting speed and feed were significant at the 95% confidence level. Further, a novel optimization tool namely the spotted hyena optimizer (SHO) algorithm was utilized to get the optimal levels of input variables. Additionally, two different modeling tools namely multiple adaptive neuro-fuzzy inference system (MANFIS) and radial basis function neural network (RBFNN) were utilized for formulating the cutting response models. Further, the average of the absolute error was estimated for each model and compared. The MANFIS modeling tool exhibited a closer prediction of outputs as compared to RBFNN, as the obtained average absolute error for each response was lower with MANFIS.
12. Kumar, V., Dewangan, H. C., Sharma, N., & Panda, S. K. (2022). Numerical prediction of static and vibration responses of damaged (crack and delamination) laminated shell structure: An experimental verification. Mechanical Systems and Signal Processing, 170, 108883. https://doi.org/10.1016/j.ymssp.2022.108883 (Impact Factor: 8.934).
Abstract
This research reported the influences of combined damage (delamination and crack) on the layered structure numerically via finite element technique in a higher-order mathematical model framework. In this regard, the modal responses and the strain energy release rate (SERR) are calculated by considering the influences of the delamination and/or crack within the flat/curved laminated structure. Moreover, the virtual crack closure technique (VCCT) has been adopted to compute the structural responses of the layer cracked composite structure, i.e., the SERR values. Further, the exactness of the present model is proven by comparing the frequency and SERR values with the previously published data from the open domain. Additionally, the model validity is certified through the different comparisons with in-house recorded experimental eigenvalues. The composite shell structures are examined for eigenvalue and SERR to assess the effects of delamination and/or crack by altering the input variables to show the applicability of the present model.
13. Kashyap, A. K., Parhi, D. R., & Pandey, A. (2022). Multi-objective optimization technique for trajectory planning of multi-humanoid robots in cluttered terrain. ISA transactions, 125, 591-613. https://doi.org/10.1016/j.isatra.2021.06.017 (Impact Factor: 5.911).
Abstract
Humanoid robots hold a decent advantage over wheeled robots because of their ability to mimic human exile. The presented paper proposes a novel strategy for trajectory planning in a cluttered terrain using the hybridized controller modeled on the basis of modified MANFIS (multiple adaptive neuro-fuzzy inference system) and MOSFO (multi-objective sunflower optimization) techniques. The controller works in a two-step mechanism. The input parameters, i.e., obstacle distances and target direction, are first fed to the MANFIS controller, which generates a steering angle in both directions of an obstacle to dodge it. The intermediate steering angles are obtained based on the training model. The final steering angle to avoid obstacles is selected based on the direction of the target and additional obstacles in the path. It is further works as input for the MOSFO technique, which provides the ultimate steering angle. Using the proposed technique, various simulations are carried out in the WEBOT simulator, which shows a deviation under 5% when the results are validated in real-time experiments, revealing the technique to be robust. To resolve the complication of providing preference to the robot during deadlock condition in multi-humanoids system, the dining philosopher controller is implemented. The efficiency of the proposed technique is examined through the comparisons with the default controller of NAO based on toques produces at various joints that present an average improvement of 6.12%, 7.05% and 15.04% in ankle, knee and hip, respectively. It is further compared against the existed navigational strategy in multiple robot systems that also displays an acceptable improvement in travel length. In comparison in reference to the existing controller, the proposed technique emerges to be a clear winner by portraying its superiority.
14. Panda, S. K., & Rana, B. K. (2022). Numerical simulation and analytical prediction on the development of entrained air filament caused by the combined effect of rotational field and free stream flow. Industrial & Engineering Chemistry Research. 61, 26, 9456–9473. https://doi.org/10.1021/acs.iecr.2c00684 (Impact Factor: 4.326)
Abstract
In this study, an attempt has been made to characterize the pattern of entrained air filament inside a liquid bath of high viscosity by employing a fully submerged horizontal rotating solid roller where the lighter phase is allowed to flow uniformly above the bath. The influence of roller rotational speed (ω), depth of submergence (h/D), strength of the crossflow (Reflow), and fluid pair (Mo) on the entrainment profile has been established numerically to report the physical insights. An open-source Gerris solver has been employed to perform this computational work. We have also described the transient dynamics of the cusp tip for various input pertinent parameters. In addition, both departure of bubbles at the tip of the steady configured cusp and the entrainment rate are predicted for different gas–liquid pairs. Interfacial configurations are also obtained as a consequence of the effect of gravitational pull. Lastly, an analytical analysis predicted successfully the obtaining of the structure of the cusp, and the predictions are quite satisfactory compared to present numerical data.
15. Mohapatra, S., Sharma, N., Dewangan, H. C., & Panda, S. K. (2022). Flutter characteristics of multi-layered composite shell panels under supersonic flow with curvature effect. Waves in Random and Complex Media, 1-19 (DOI: 10.1080/17455030.2022.2083719) (Impact Factor: 4.051)
Abstract
This study presents the finite element (FE) solutions to the aeroelastic flutter behaviour of multi-layered composite shell panels with flat and cylindrical geometry under supersonic flow based on third-order shear deformation mid-plane kinematics. The shell panel is discretized by a nine-noded isoparametric shell element with nine nodal degrees of freedom. The effect of the aerodynamic load is incorporated through first-order piston theory. The numerical model’s accuracy and validity are justified by comparing the present solutions (free vibration frequency, coalescence frequency, and the corresponding critical aerodynamic pressure) with the existing numerical results. Also, the current natural frequencies are compared with the values from in-house experimental tests. The influence of parameters such as the flow angle, fibre orientation, material anisotropy, thickness ratio, and curvature ratio on the supersonic flutter boundaries of the shell panels subjected to simply supported and clamped conditions is investigated. The results are deliberated in detail, and it is observed that the fibre orientation and material anisotropy affect the flutter boundary differently under the simply supported and clamped conditions. Moreover, the first coalescence is greatly influenced by the flow angle instead of the curvature of the curved shell panels.
16. Sahu, P., Sharma, N., Dewangan, H. C., & Panda, S. K. (2022). Theoretical Prediction and Experimental Validity of Thermal Frequency Responses of Laminated Advanced Fiber-Reinforced Epoxy Hybrid Composite Panel. International Journal of Structural Stability and Dynamics, 2250088. https://doi.org/10.1142/S0219455422500882 (Impact Factor: 2.957)
Abstract
Thermal frequency responses of the hybrid laminated composite panel are theoretically computed using the finite element model and for the first time compared with in-house experimental data. The structural model for hybrid panel is derived using higher-order displacement polynomial functions (to maintain the necessary stress/strain continuity) and discretized through the isoparametric finite elements. Moreover, the elastic properties of the composite are evaluated suitably including thermal and physical parameters of the advanced fibers (Glass/Carbon/Kevlar) with the help of experimentations and numerical tool (via ABAQUS using mean-field homogenization). The variation of modal responses due to the change in temperature increment is computed through a generic computer code generated via the higher-order mathematical model. The numerical frequency values are compared with the earlier published numerical results and the experimentally recorded eigen frequencies. The experimental verifications related to the end boundaries indicate that the incorporation of the clamped boundary for one edge doubles the frequency, whereas the fraction of Kevlar fiber does not influence the stiffness (due to longitudinal modulus) parameter irrespective of the temperature change. Further, the conclusive understandings of the hybrid composite structural panel due to the inclusion of different advanced fibers and other design parameters (geometry, boundary and temperature) are deliberated in detail.
17. Mohapatra, B., Tripathy, S., Singhal, D., & Saha, R. (2022). Significance of digital technology in manufacturing sectors: Examination of key factors during COVID-19. Research in Transportation Economics, 93, 101134. (Impact Factor: 2.904)
Abstract
The Covid-19 pandemic has been the center of human existential chaos throughout the world, which also has affected the manufacturer in an extraordinary and unexpected way. With the decline in demand, supply, and workforce the industries are driven into the gloom. The concerned research objective is to explore the factors which impact manufacturing throughout the world during the epidemic of Covid-19. Further, it delineates the usage of advanced digital technologies like artificial intelligence (AI), big data analytics (BDA), and internet of things (IoT) to bring on solutions/approaches to evolving to pandemic-constrained manufacturing. An overall of twelve key factors is determined from extensive literature reviews which are categorized into challenges and solutions. Here, ISM methodology has been used to establish the interrelationship among identified twelve challenges and solutions. Further, MICMAC analysis has categorized them according to their driving and dependence power. The consequences display the absence of autonomous factors whilst efficient supply chain, centralized decision making, product diversification, and JIT along with revenue generation turn out to be significant dependant factors. The facilitators like digital technologies are the pre-cursors to the ultimate solution of revenue generation and termed preliminary solutions. The outcomes of this research will suggest eventual policy recommendations for industry leaders to progress manufacturing within Covid-19 constraints. It will offer a sturdy base for manufacturers around the world to tune to the new digital transformation of the production scenario.
18. Nalla, B. T., Devarajan, Y., Subbiah, G., Sharma, D. K., Krishnamurthy, V., & Mishra, R. (2022). Investigations of combustion, performance, and emission characteristics in a diesel engine fueled with Prunus domestica methyl ester and n‐butanol blends. Environmental Progress & Sustainable Energy, e13811. (Impact Factor: 2.824)
Abstract
The chief objective of this study is to utilize non-edible, carbon-rich oil derived from Prunus domestica seeds as blended fuel. The combustion efficiency of derived blends shall further be enhanced by blending higher alcohol into biodiesel/diesel blends. This work details the impact of effectively utilizing waste and non-edible oil to replace fossil fuels partially. In this study, the P. domestica is trans-esterified to methyl ester and blended with diesel at 20%. Further to enhance the ignition nature, butanol, higher alcohol, is blended to P. domestica biodiesel/diesel blends at 5% and 10%. The ignition pattern of the modified fuels is extensively studied and compared with diesel in a stationary research diesel engine. This study involves four fuel samples, namely, neat P. domestica methyl ester and is termed PDME. 20% of PDME is blended with 80% diesel is referred to as PDME20. 20% of PDME with 5% n-butanol and 75% diesel is termed PDME20Bu5D75, 20% of PDME with 10% n-butanol and 70% diesel is termed as PDME20Bu10D70 and diesel. Addition of PDME and butanol at different blends found miscible with diesel. PDME and butanol provided a suitable time for reaction and mixing, complete combustion, higher O2 content, and rich fuel-air mixture, resulting in lower emissions than diesel. Further, butanol aided better atomization, effective combustion and resulted in higher efficiency with lower fuel consumption. Adding butanol also lowered the viscosity and improved the mixing process, and produced better in-cylinder pressure and heat release rate.
19. Aurtherson, P. B., Hemanandh, J., Devarajan, Y., Mishra, R., & Abraham, B. C. (2022). Experimental testing and evaluation of coating on cables in container fire test facility. Nuclear Engineering and Technology, 54(5), 1652-1656. (Impact Factor: 2.817)
Abstract
Fire tests were conducted on cables using fire-retardant paint employed in nuclear power plants that transmit electrical power, control and instrument signals. The failure criteria of various power and control cables coated with fire retardant coating at three different coating thicknesses (∼0.5 mm, 1.0 mm & 1.5 mm) were studied under direct flame test using Container Fire Test Facility (CFTF) based on standard tests for bare cables. A direct flame fire test was conducted for 10 min with an LPG ribbon burner rated at ten by fixing the cable samples in a vertical cable track. Inner sheath temperature was measured until ambient conditions were achieved by natural convection. The cables are visually evaluated for damage and the mass loss percentage. Cable functionality is ascertained by checking for electrical continuity for each sample. The thickness of cable coating on fire exposure is also studied by comparing the transient variation of inner sheath temperature along the Cable length. This study also evaluated the adequacy of fire-retardant coating on cables used for safety-critical equipment in nuclear power plants.
20. Panigrahi, R. R., Panda, A., Sahoo, A. K., Kumar, R., & Mishra, R. R. (2022). Turning performance analysis and optimization of processing parameters using GRA-PSO approach in sustainable manufacturing. Proceedings of the Institution of Mechanical Engineers, Part E: Journal of Process Mechanical Engineering, 09544089221093309. (Impact Factor: 1.822)
Abstract
The main aim of this research work is to examine the impact of input process factors (cutting speed, feed rate, and depth of cut) on machining characteristics (arithmetic mean surface roughness, tool flank face wear and tool chip interface temperature) and further to optimize during turning of Incoloy alloy 800. The cutting tool used was PVD multilayer coated (TiAlN-TIN) carbide insert. The experiment was performed based on Taguchi L27 methodology with a focus on the sustainability of turning. Sustainable manufacturing is considered for accomplishing overall efficiency with regard to economic, environmental and social aspects. The ANOVA (Analysis of Variance) was employed to assess the contributions of input process variables on cutting variable outputs. Further, the main effect diagrams exemplified the influences of main parameters on response variables. ANOVA analysis results demonstrated that the feed rate was the most leading factor that affects average surface roughness. The relationship(s) among input process factors and the evaluated measured outputs are determined using a quadratic regression model. Taguchi grey relational analysis has been implemented to trial results so as to optimize responses. The results revealed that the grey relational grade is significantly improved (0.308) through the setting of optimal parametric combinations. This integrated Grey–Taguchi approach was established quite effectual for simultaneously optimization of multifaceted machining output responses of turning process. This study provides a novel strategy to develop the machining efficiency of Incoloy 800 steel toward the improvement of sustainable processes and provide suitable applications in aerospace industry.
21. Shah, K., & Mishra, R. (2022). Modelling and optimization of robotic manipulator mechanism for computed tomography guided medical procedure. Scientia Iranica, 29(2), 543-555. (Impact Factor: 1.416)
Abstract
Although industrial robots are common, a higher degree of manipulability might be required to expand the applications of manipulators in the field of medicine. Modifying the mechanical design of a robot as per the workspace can be perceived as an optimization problem. Hence, a novel spatial manipulator is designed for a diagnostic apparatus using different optimization algorithms. Standard Genetic Algorithm (SGA) and GA (Genetic Algorithm) with hybrid functions like pattern search (PS) and fmincon are proposed to optimize the link lengths of a 3degrees of freedom (DOF), 6-DOF, and novel 9-DOF hybrid redundant manipulator. A 9-DOF robot is designed to manipulate a needle in CT machine environment. The fitness function for all the manipulators is formulated using forward kinematic equations according to their workspace. Limits and constraints of each link are decided beforehand. A comparative study between all the hybrid GA functions is performed. MATLAB is used to solve and train the proposed GA method for optimizing the link lengths. Results show that GA with PS provides better-optimized link lengths for a 3-DOF and 9-DOF manipulator while fmincon is well suited for a 6-DOF robot manipulator. Workspace and dead zone analysis is also performed using the optimized link lengths obtained.
22. Kumar, R., Pandey, A., Sahoo, A. K., & Rafighi, M. (2022). Investigation of machinability performance in turning of Ti–6Al–4V ELI alloy using Firefly algorithm and GRNN approaches. Surface Review and Letters, 2250075. (Impact Factor: 1.240)
Abstract
Ti–6Al–4V ELI alloy is one of the most familiar materials for orthopedic implants, aeronautical parts, marine components, oil and gas production equipment, and cryogenic vessel applications. Therefore, its appropriate quality of finishing is highly essential for these applications. But the characteristics like lower modulus of elasticity, lesser thermal conductivity, and high chemical sensitivity placed it in the categories of difficult-to-cut metal alloys. Also, tooling cost is one of the prime issues in the machining of this alloy. Therefore, this research is more inclined to use a low-budget uncoated carbide tool in turning the Ti–6Al–4V ELI alloy. Also, the selection of suitable levels of machining parameters is highly indispensable to get the appropriate surface finish with a low tooling cost. So, the L16 experimental design is utilized to check the performances of the uncoated carbide tool in the turning tests. The performance indexes like surface roughness (Ra), flank wear of tool (VBc), and material removal rate (MRR) are measured and studied with the help of surface plots and interaction plots. Further, the Firefly Algorithm optimization is employed to find the optimal cutting parameters and cutting response values. The local optimal values of the input parameters a, f, and Vc are estimated as 0.3241mm, 0.0893mm/rev, and 82.41m/min, respectively. Similarly, the global optimal values for the responses Ra, VBc, and MRR are reported as 0.6321μm, 0.09253mm, and 24.61g/min, individually. Additionally, to predict the responses, Generalized Regression Neural Network (GRNN) modeling is employed and the average absolute error for each response is noticed to be less than 1%. Therefore, the GRNN modeling tool is strongly recommended for various machining applications.
23. Chaudhuri, S., Mohanty, R. L., & Mishra, V. K. (2022). Convective heat transfer in electromagnet hydrodynamic flow of third grade fluids through large parallel plates: a study on effect of parametric variation on thermal characteristics. Sādhanā, 47(2), 1-14. (Impact Factor: 1.214)
Abstract
Electromagnet hydrodynamic flow and heat transfer of a non-Newtonian third grade fluid through two parallel plates of large width are studied for both heating and cooling. The plates are subjected to uniform heat fluxes. A magnetic field and an electric field are externally imposed. The effects of viscous dissipation and Joule heating are included in the analysis. The non-linear equations governing the physical situation are solved by employing the Least Square Method (LSM), a semi-analytical technique widely applied for solving non-linear problems. For implementing the least square method, the presence of any small parameter is not required. Non-dimensional velocity and temperature distributions are obtained and the effects of the third grade fluid parameters, Hartmann number, electric field parameter, Brinkman number on the velocity, temperature, and Nusselt number are discussed. The results imply that the Nusselt number reverses its sign when the Brinkmann number reaches a critical value. The bulk mean temperature decreases so much that the difference between the wall temperature and the bulk mean temperature becomes negative, which results in a negative Nusselt number (indicating heat transfer from the fluid). In the case of heating, the Nusselt number increases with the Hartmann number for all values of the third grade fluid parameter.
Conference papers
1. Meher, J., Nayak, B. B., Panda, A., Kumar, R., & Sahoo, A. K. (2022). Recent research development of CNC based milling machining conditions: A comprehensive review. Materials Today: Proceedings. Volume 62, Part 6, 2022, 3983-3989. https://doi.org/10.1016/j.matpr.2022.04.582
Abstract
With the advancement in manufacturing technologies, various improved machining processes have been developed and CNC based milling process is also one of the front line machining providing more advantages than another traditional process. With the substantial growth of machining processes, machining characteristics also change according to the tool and work materials, tools being used types of machining process utilized, etc. due to improved surface finish with excellent dimensional accuracy with minimum tool wear. In this context, these output parameters need to get fulfilled by optimizing the input parameters like cutting speed, feed rate, and depth of cut during machining of the cutting environments like dry machining, flood cooling, Minimum Quantity Lubrication (MQL). Here some of the advanced cutting conditions based on CNC milling considering various types of materials are reviewed. This will assist researchers to focus on further exploring CNC based Milling process.
2. Tarai, H., Samal, P., Vundavilli, P. R., & Surekha, B. (2022). Experimental study of microstructural and mechanical characterization of silicon-bronze copper alloy (C87600) hybrid composites reinforced with SiC-Gr particles by stir casting. Materials Today: Proceedings. Volume 62, Part 6, 3221-3225. https://doi.org/10.1016/j.matpr.2022.04.218
Abstract
In this study, the fabrication of copper-based hybrid metal matrix composites using the stir casting process was conducted. Ceramic particles i.e. SiC and graphite are considered as reinforcements for the fabrication of hybrid composites. The microstructure of composites was analyzed using Field emission scanning electron microscope (FESEM) and X-ray diffraction (XRD) spectroscopy. Uniform dispersion of the reinforcements throughout the matrix has been validated from the FESEM micrographs. The Vickers microhardness test was performed to examine the microhardness and its variation with respect to the reinforcement content. It was found that the microhardness value was found to be increased with an increase in reinforcement content. The tensile test of the fabricated composites was conducted using a Universal testing machine, and its variation with respect to the reinforcements is analyzed. It was observed that the tensile strength of the copper hybrid composites was enhanced with the increase in the reinforcement content. The composites with 8% SiC and 1% Gr had exhibited a maximum increase of 34% in the ultimate tensile strength as compared to the base matrix alloy. It is highly anticipated that the fabricated composites with their enhanced strength are suitable for potential applications in various structural applications.
3. Sahu, R. K., Das, R., Routara, B. C., Nayak, B. B., & Sahu, S. (2022). Multi-hole extrusion process: A review. Materials Today: Proceedings. Volume 62, Part 6, 3522-3527. https://doi.org/10.1016/j.matpr.2022.04.349
Abstract
Extrusion process has played a big role in the metal forming industries for production of many metallic materials of different cross-sections. The die design, lubrication conditions and other parameters are well established with conventional extrusion process. Multi-hole extrusion process uses die with more than one orifice and accordingly more than one product can be obtained during extrusion. The extruded parts obtained from multi-hole extrusion process show different length, mechanical properties as the effect of different process parameters are different. The present review work focuses multi-hole extrusion and its significance to industrial revolution. This review work will provide insights of different methods of understanding the process, effect of different process parameters on extruded product length, product quality and mechanical as well physical properties.
4. Sinha, A., Kar, S. P., & Swain, A. (2022). An experimental study on effect of titanium oxide coated heater substrate on pool boiling enhancement. Materials Today: Proceedings. Volume 62, Part 10, 5948-5955. https://doi.org/10.1016/j.matpr.2022.04.682
Abstract
The present experimental study indicates the effect of coating on the enhancement of heat transfer during pool boiling. For this, the aluminium heater substrate of 22 mm * 20 mm was coated with titanium oxide using high velocity oxy fuel (HVOF) method. The coated surface was then used to heat aqueous solutions of acetone, isopropanol, ethanol and distilled water respectively. Simultaneously, heat transfer coefficient (HTC) and excess temperature (dT) were also obtained using aluminium heater substrate without coating. The boiling parameters during coating and non-coating were kept same so that the HTC and dT obtained can be used for comparative study. The heat transfer parametric study was then conducted and the results were presented in graphical form.
5. Jena, S. M., Sant, S. M., Mishra, R., Nayak, S. K., & Nayak, S. (2022). Design and analysis of flying u a V drone for sanitization purpose. Materials Today: Proceedings. Volume 62, Part 12, 6583-6589. https://doi.org/10.1016/j.matpr.2022.04.580
Abstract:
Drones are unmanned aerial vehicles that can perform a variety of tasks and can be employed in any sector. The major focus of this work is to show how drones/UAVs may combat the issues faced by COVID-19. With constructive qualitative research, this work is structured to provide insights into theory techniques. Using solid work Drones model is created and using Ansys static and explicit dynamic analysis are done. The fundamental contribution of this paper is to design a drone for sanitization and screening. This research will be extremely beneficial to people in this pandemic situation.
6. Rajan, K. M., Sahoo, A. K., Routara, B. C., Panda, A., & Kumar, R. (2022). A review on various approaches of 3D printing of Ti-Alloy. Materials Today: Proceedings. Volume 62, Part 6, 3865-3868. https://doi.org/10.1016/j.matpr.2022.04.532
Abstract
The demand for 3D metal components with complex shape and high quality with timely delivery is the focus for the development of additive manufacturing known as 3D printing. 3D metal printing is becoming very popular day by day among manufacturing industries, young engineers and “startups” due to the flexibility of realization of ideas. 3D metal printing is growing into a revolutionary technology in today’s world due to application in various industries such as aerospace, biomedical and automotive sectors etc. Fabrication and development of net-shape metallic components of complex geometric shape is the key strength of 3D metal printing where layer-by-layer metal powder is deposited from a 3D printer through computer-aided design. Powder metallurgy is the traditional method to fabricate titanium alloy whereas laser additive manufacturing is the emerging technology now-a-days. The advantage of 3D metal printing of titanium-based components is light in weight, cost effective approach and reduces material loss. The growth of last ten-year’s data shows the emerging trends of 3D printing as future disruptive technology with application in every field of life such as food, cloths, machines, building, biomedical implants and even human body parts. This paper overviews on various approaches to 3D printing of Titanium alloy (Ti-6Al-4V) on recent development with fabrication method, limitations and application and finally summarizes the findings. It is evident from the observations that the 3D printed titanium alloys produced through laser melting yields higher strength and yield point compared to conventional methods. Finally, further research in 3D metal printing has been presented.
7. Khatai, S., Sahoo, A. K., Kumar, R., & Panda, A. (2022). On machining behaviour of various cutting inserts: A review on hardened steel. Materials Today: Proceedings. Volume 62, Part 6, 2022, 3485-3492. https://doi.org/10.1016/j.matpr.2022.04.301
Abstract
Cutting tool plays an important criterion for the overall performance of machining to achieve better tool-life, superior surface finish along with immense productivity. The evolution of cutting temperature along with increased cutting parameters accelerates the plastic deformation of insert tip, cutting edge breakage and thus affects the surface quality. Built-up-edge (BUE) formation also enhances rapid tool wear, fluctuations of cutting forces, and vibration. Therefore in modern manufacturing to enhance productivity considering good surface quality, there is striving for innovation and research in the area of novel cutting tool materials. Hard machining emerges as a newer process alternative to traditional grinding performance where popular cutting tool materials used as CBN (Cubic Boron Nitride), ceramics, and coated carbides etc. The benefits of hard machining serve as reduction of the manufacturing cycle, cost, and environmental friendly. Thermal softening and reduction of shear stress due to the rise of cutting temperature enable hard machining easier under dry environment compared to flood cooling. However, tool wear and surface roughness deteriorates and thus reduces tool life due to frequent failure of cutting edge. Thus in the current review, the performance of cutting tool materials during machining hardened steels is focused. Moreover, a proper selection of cooling and lubrication strategy can prolong the tool life and surface finish. Different hard thin layer coatings on carbide tools enhance the machining performance due to thermal barrier, abrasion, and diffusion resistance properties. Due to techno-economical feasibility, coated carbide cutting tools are extensively used during hard machining in recent years which has been developed by CVD/PVD method.
8. Akeel, A. M., Kumar, R., Chandrasekhar, P., Panda, A., & Sahoo, A. K. (2022). Hard to cut metal alloys machining: Aspects of cooling strategies, cutting tools and simulations. Materials Today: Proceedings, Volume 62, Part 6, 3208-3212. https://doi.org/10.1016/j.matpr.2022.04.053
Abstract
Machining hard-to-cut alloys undergo severe tool wear and poor surface finish, making it challenging for the machinist. The emergence of higher temperature in the machining of hard-to-cut alloys (hardened steel, Ti-alloys, Ni-base alloys, etc.) was seemed to be the main issue for the machining industries. Over the past decade, several cooling strategies and improved cutting tools material were adapted to enhance the machining performances of hard-to-cut metal alloys. In addition, these alloys are costlier; hence without wasting time, energy, and cost, many researchers have worked on simulation modeling to interoperate the feasibility of utilized cooling strategy, cutting tools, and level of machining input parameters. The present study gathered the relevant information from the literature and presented a brief review on cutting fluid, cutting tools, and simulation methods in machining difficult-to-cut metal alloys. This study may be helpful to the learners to select appropriate cutting fluid, cutting tool, and simulation method for machining of hard to cut metal alloys.
9. Behera, D. D., Das, S. S., Mishra, S. P., Mohanty, R. C., Mohanty, A. M., & Nayak, B. B. (2022). Simulation of solar operated grass cutting machine using PVSYST software. Materials Today: Proceedings. Volume 62, Part 6, 2022, 3044-3050. https://doi.org/10.1016/j.matpr.2022.03.175
Abstract
The objective of this paper is to use PVSYST software to model solar-powered grass-cutting equipment. The usage of solar-powered grass-cutting equipment has no negative environmental consequences when compared to a diesel-powered grass-cutting machine. The solar-powered grass-cutting machine is a renewable energy device that will assist the recipients in swiftly mowing the grass. The solar grass-cutting machine was a quick process of cutting and proper system parameters used for doing simulation in PVSYST software. A simulation study has been précised and obtained from a solar off-grid system. Simulation parameters such as latitude of the location, sizing, and specification of solar panel, battery, charge controller, dc motor have been taken to get the simulation result. Simulation results such as performance ratio and solar fraction have been obtained throughout the year and are maximum values reach 0.171 and 0.2 respectively in April.
Patents Filed:
Title: Apparatus to measure heat transfer of nanoaerosol and a method thereof
Application No. 202231038094 (Indian)
Date of Filing: 30th June 2022
Inventors: Mrs. Vidyasri Khadanga, Dr. Sayantan Mukherjee, Dr. Purna Chandra Mishra & Dr. Shanta Chakrabarty
Consultancy Services
S.No. | Organisation | Work Description | Status |
1 | Adani Defence Systems & Technologies Limited, Ahmedabad | Development of aero-engine design, development and manufacturing capability in India. | 100 % completed. |
2 | Corrosion Protection Private Limited, Cuttack | Automation in the Seam welding process of LPG cylinder manufacturing | 100 % completed. |
3 | AKON Group of Industries | Design, development and manufacture of thermal screening door to differentiate between Covid & non-Covid patients | 100 % completed. |
4 | Bharat Dynamics Limited (BDL), Vizag | Design and supply of Vendor Management Software- Phase 1 | Received |